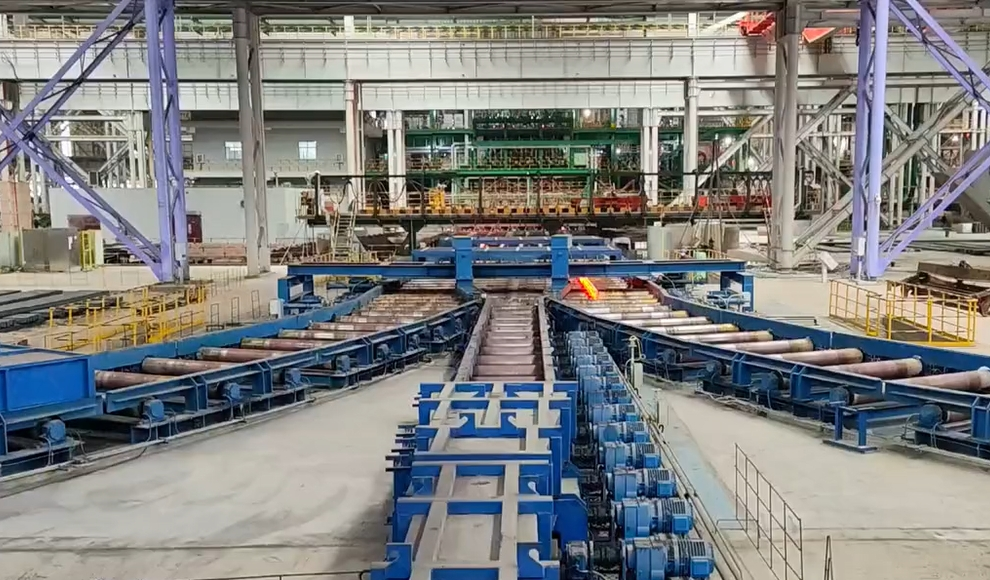
Direct rolling technology involves the direct rolling of steel billets from the continuous casting machine into final products without any heating or reheating processes. The achievements made in the industrialization of direct rolling technology exhibit extensive adaptability and can be applied to both new and existing production lines.
I. Broad Adaptability:
1.Applicable to new rod lines and the renovation of existing production lines.
2.Suitable for both single-line and multi-line correspondences in steelmaking.
3.Distance between steelmaking and rolling not exceeding 500m, expandable to 700m using third- generation ultra-high-speed heavy-duty roller conveyors.
4.Elevation difference between steelmaking and rolling not exceeding 10m.
II. Key Points of Independent Direct Rolling Technology:
Integration of direct rolling technology and equipment industrialization achieves a direct rolling rate of up to 99.9%, with a maximum monthly output of 154,200 tons and a maximum daily output of 5,300 tons, meeting the demands of high-volume production line refurbishment.
1.Achieved high quality:
a. Achieved temperature differentials of within 30°C for different flows, speeds, exit times, and specified length billets without secondary heat sources or insulation.
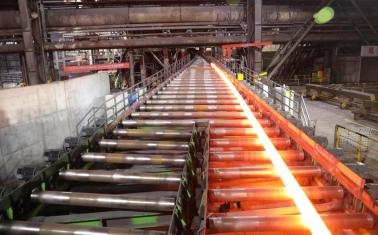
b. Innovated the “core-edge ratio” theory, effectively utilizing large temperature differentials to achieve significant alloy savings.
c. Improved stability of weight deviation by 0.7%, producing a wide range of products including HPB300, HRB400E(F), and HRB500E(F) for high-wire, bar, and high-speed bar production lines.
2.Achieved inherent greenness:
Completely eliminated the use of any heat sources, eliminating heating processes from the process, resulting in significant reductions in carbon, SO2, NOx emissions, and other pollutants.
3.Achieved digitalization:
Each billet is assigned a digital ID, enabling online quality control, temperature control, and energy consumption control.
a. Highly integrated digital quality control system for direct rolling, ensuring real-time adjustment of temperature and quality consistency for each steel product.
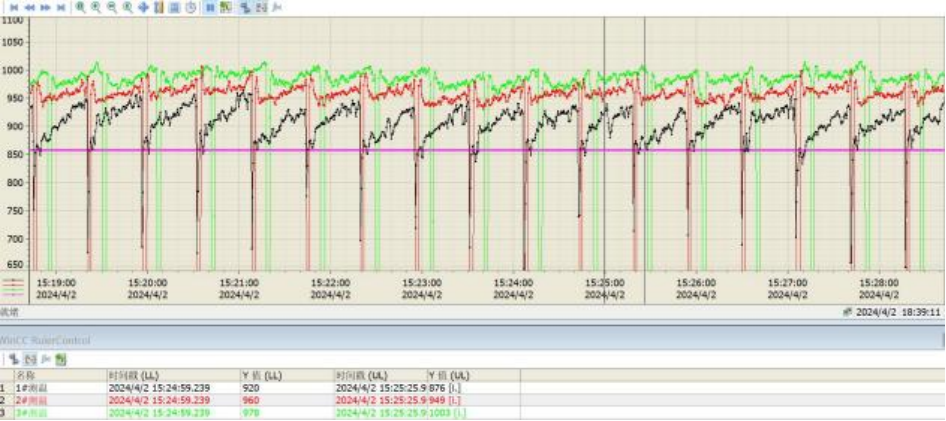
b. System integration of digital high-speed heavy-duty roller conveyors, reducing the time from continuous casting to rolling to just 50 seconds.
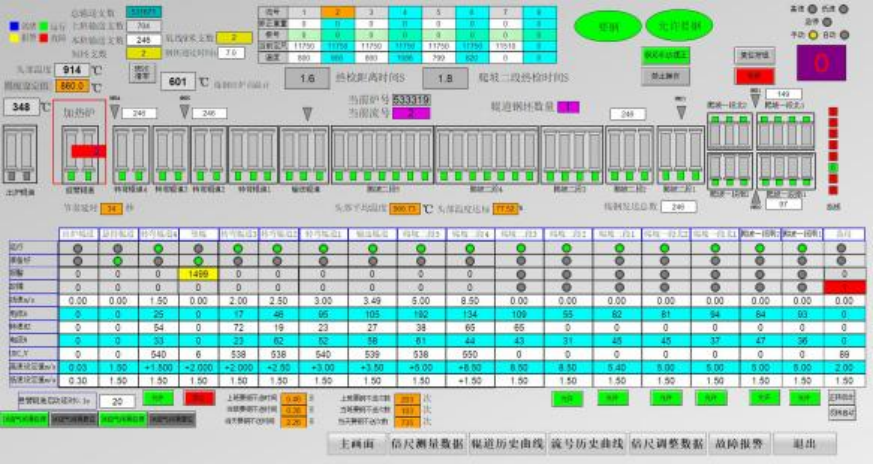
c. Achieved dynamic adjustment of length for each billet-steel product pair under the “full-length requirement,” with a fixed-length rate of 99.80%.
d. Implemented dynamic allocation of rolling mill torque, reducing theoretical power consumption by 5-10%.
4. Investment Returns:
a. Significant efficiency gains: The tonnage benefit is no less than 30 yuan per ton.
Efficiency gains at a certain steel plant example are as follows:
1). Savings in heating costs and yield improvement alone yield a benefit of 42.36 yuan per ton.
2). Total benefit from all aspects amounts to 52.47 yuan per ton.
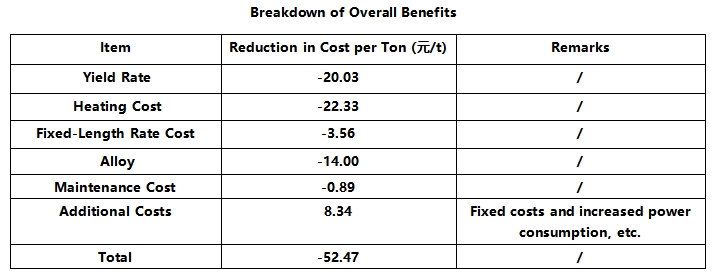
b. Rapid investment returns:
1). Case one: A steel plant invested 28.5 million yuan in direct rolling transformation, achieving a direct benefit of 52.47 yuan per ton, with a payback period of only 0.32 years.
2). Case two: A steel plant with an estimated investment of 55 million yuan expects a payback period of 1 year.